Brief Analysis of RTLS System In Factory Plant
Published on Saturday, Nov 14, 2020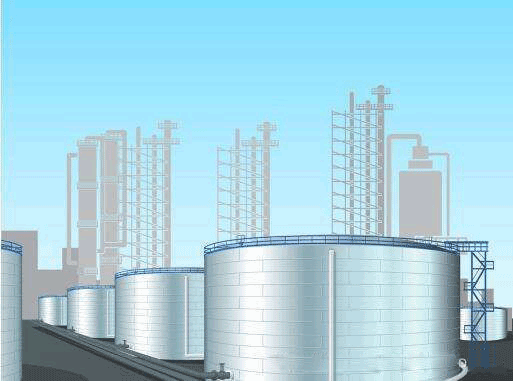
Current real time location system mainly refers to outdoor and indoor scenes. There are many products are used for RTLS, including UWB, RFID, GPS and others. According to application scene, they are divided into assets tracking, personnel tracking, logistics tracking and others. After years of development, real-time location technology accuracy, coverage scale, capacity, delay and other objectives are all being optimized. With the increase of industry maturity, the use of RTLS is growing rapidly, especially in occupations such as automobiles and medical care. The RTLS market is estimated to reach 6.3 billion US dollars in 2022, with a compound annual growth rate of 28% from 2016 to 2022. High industrial growth and big data transformation of enterprises are the main factors driving the RTLS market. High costs, environmental disturbance, system incompatibility, and lack of uniformity are the deterrent factors for the market.
From the perspective of users, RTLS brings four main benefits to enterprises: improving economic efficiency, such as RTLS in warehousing and logistics. Reduce the risk of safety accidents, such as early warning under danger area and post-disaster rescue. Provide technical support for refined management, such as personnel and asset RTLS, electronic fences, etc. The workshop is digitalized and transparent in work shop, such as intelligent material box, AGV, automatic guidance of mobile robots in the factory etc.
The real-time location system for chemical plant personnel is a flexible and scalable location platform based on a simple architecture network, which can provide components and services required for customized positioning solutions and provide a one-stop RTLS solution.
System hardware infrastructure: active tags fixed on the device automatically send wireless signals at a predefined distance. Four or more anchored base stations receive signals and send them to the positioning server through the positioning gateway.
Active tag: It is bound to the processed target (workpiece, robot, vehicle, person, etc.) and can send wireless signals at a specified time and distance. The active tag can also be equipped with a data interface to directly transmit detailed position information to the local control system, or provide necessary sensor data to the upper system.
RFID Reader/Anchor/Base station: accept the active tag wireless signal, attach its coordinates and time stamp, and transmit tag incidental data. After at least three mutually synchronized anchoring base stations, the three-dimensional positioning of the active tag can be completed with an accuracy of centimeter level.
Gateway: used to pack all recorded data and transmit it to the upper location server, and at the same time can act as an anchor base station.
Location algorithm/server: calculate the real-time position coordinates of the active tag, and define and modify the types of things related to the position through the rule engine.
Location application software: a software system used to calculate the real-time position of detailed active tag, using multi-mode blending location technology, and passing through a designated interface, according to the rules that can be defined and configured to transmit detailed information to the upper system.
Service integration: location information and things are passed to the upper system for automatic control, data statistical analysis, process optimization and adjustment.
In the chemical plant personnel location system, the real-time location system serves a variety of upper intelligent systems, 4W (Where, When, Who, What, What) positioning data from RTLS and the upper system ERP/MES/WMS H (how to do, how to operate) transaction data integration, linkage work, maximize the use of production resources, improve on-site processing power and accuracy.